Step by Step Manufacturing Process
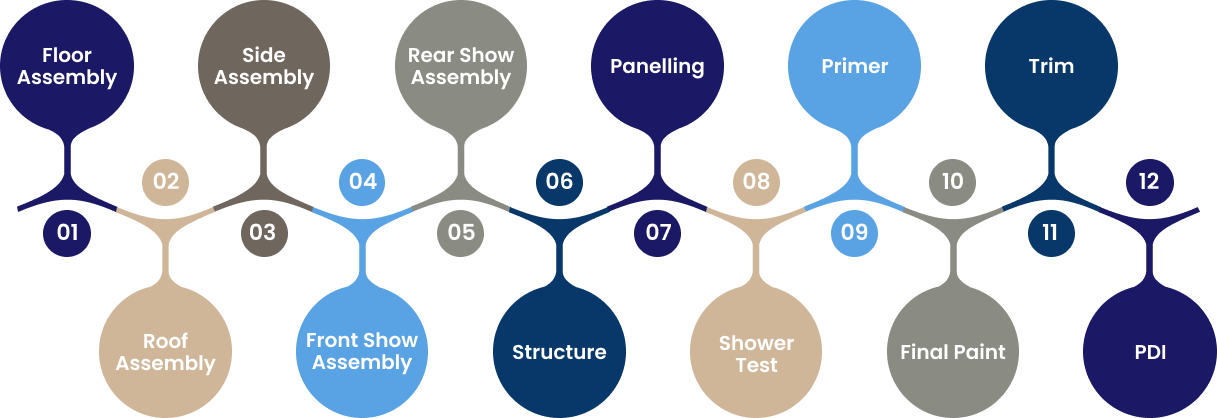
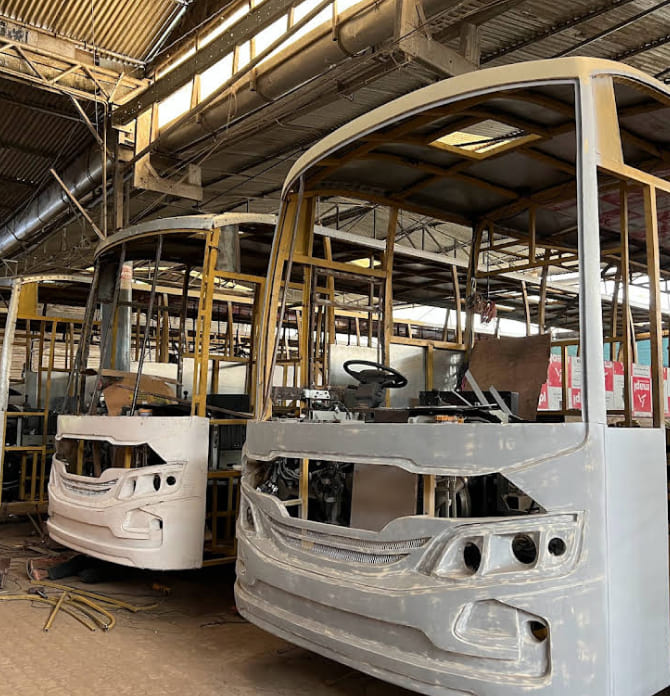
The bare chassis is inducted into the workshop and the flooring, composed of rolled channels, is mounted on the vehicles by U bolts.
The side structure and the roof structure consisting of carefully-engineered steel pressed sections of different thicknesses with strongly gusseted joints and pre-assembled on jigs and fixtures are mounted on to the vehicles forming sturdy steel "fortress" around the passengers. The strength of this construction ensures the greater life span of the vehicle.
Each and every structural component is carefully phosphated using the ten tank process recommended by ICI and three coats of anti-rust paint are then applied to prevent corrosion.
Once the structure is assembled together the entire structure is given another coat of anti-rust paint before the panelling work begins.
Once the structure is assembled together the entire structure is given another coat of anti-rust paint before the panelling work begins.
The flooring is made either of aluminium, chequered plate or marine plywood covered with vinyl material. The side panels may be of either plastic coated aluminium sheets or plush upholstery fabric and the exterior roof is made of aluminium panel riveted on to the steel superstructure.
Before the fitment of interior roof panels, the vehicle is water tested under a shower of water resembling artificially simulated weather condition, in order to check for leakages before the fitment of the roof panels.
The doors and other fitments are fitted on to the vehicles, then the vehicle proceeds for painting process.
The painting process consists of one coat of each primer, 4 coats of primer surface and 3 coats of finished paints. All vehicles are spray painted in a pressurized paint booth and baked to a temperature of 70 degrees in oven.
The windows and other retro-fits are fitted on to the vehicles. Before delivery the vehicle is again water tested to check for water leakage into the vehicle.
Stringent quality control checks are carried out before the final dispatch of the vehicle, so that the vehicle leaves the workshop premises in the best condition.
We also offer a complete range of seats ranging from those required in a standard city bus to fully reclining seats in a choice of attractive colours.
Road testing is carried out to ensure that the vibrations and noise within the vehicle are non- existent. The entire cycle for the production of one complete vehicle ranges from approximately 3 to 4 weeks for a standard bus to 6 to 8 weeks for luxury bus and 8 to 10 weeks for an air-condition bus.
All our products are totally indigenously developed which makes our services more cost effective as we have a better insight into the prevailing conditions.
Facilities Available
-
In-House Design Facility
-
In-House Passenger Seat Manufacturing Facility
-
Shower Test
-
In-House FRP Component Manufacturing
-
Pre-Treatment Units
-
In-House Windows & Doors Manufacturing
-
Paint Booth
-
Press Shop with De-Coiling and Rolling Units
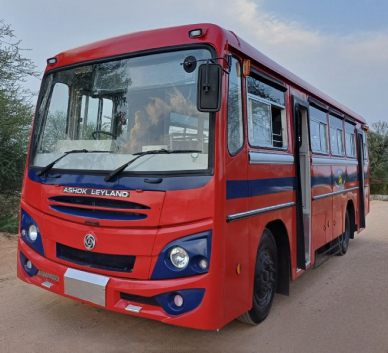